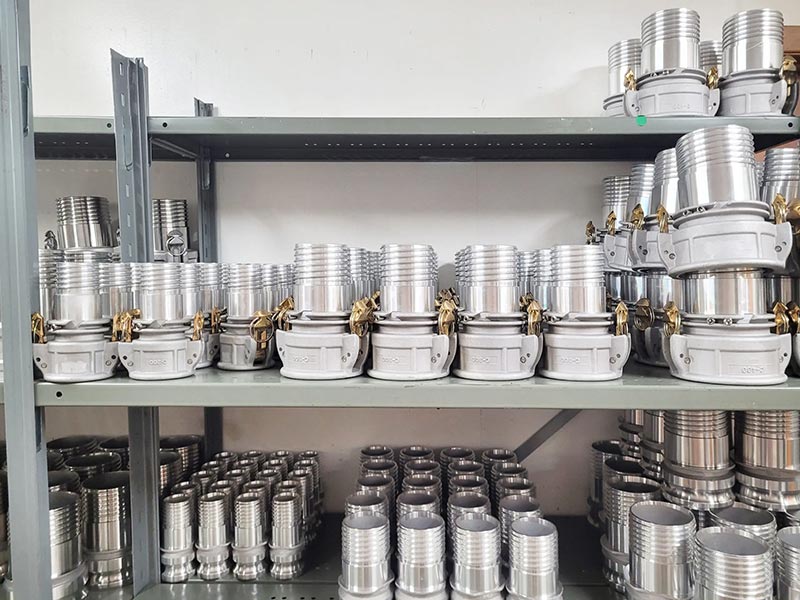
Introduction
Composite hoses are integral to numerous industries, providing a versatile and lightweight solution for transferring various liquids and gases. Thanks to its multiple layers of thermoplastic and thermosetting polymers, the hose is reinforced with inner and outer wire helixes.
The unique design allows them to handle various applications, from chemicals and petroleum products to food and pharmaceuticals. However, like any equipment, composite hoses require regular maintenance to perform at their best and ensure safe operations.
What Is a Composite Hose?
A Composite Hose is a highly flexible conduit engineered to transport a wide range of media, ensuring optimum safety and reliability. Its construction involves combining multiple layers of spirally-wrapped thermoplastic fabrics and films, firmly secured by an inner and outer wire helix made of metal.
The hose gains exceptional durability and resistance to diverse substances by blending various materials. The inner layers are specifically designed for chemical resistance, while the outer layers provide added protection against abrasion and environmental elements.
Why Proper Maintenance Is Crucial for Composite Hoses?
Effective maintenance is vital for ensuring composite hoses’ optimal performance and longevity. Several reasons underscore the importance of regular upkeep:
- Safety: Composite hoses handle hazardous materials, and any failure could result in leaks or spills, endangering personnel and the environment.
- Cost-Efficiency: Proper maintenance helps prevent premature wear and damage, reducing the need for frequent replacements and associated costs.
- Regulatory Compliance: Many industries have strict regulations governing the safe handling and transportation of materials, making maintenance necessary to meet compliance requirements.
Tips for Maintenance
Routine maintenance can significantly extend the service life of composite hoses and safeguard their functionality. Here are some essential tips:
1. Visual Inspection of the Hose and Fitting
Regularly inspect the composite hose for signs of wear, such as cracks, bulges, or visible damage. Check the fittings for proper attachment and any indications of leaks or corrosion.
2. Visual Inspection of Related Hose Assembly Components
Examine other hose assembly components, including couplings, gaskets, and clamps. Ensure they are in good condition and free from defects compromising the hose’s integrity.
3. Functional Evaluation of the Hose
Conduct functional tests on the composite hose to assess its performance under operating conditions. This may involve simulating the flow of media to identify potential issues.
4. Hose Replacement Timeframes
Establish a regular replacement schedule for composite hoses based on usage frequency, type of media transferred, and environmental conditions. Replace hoses before they reach the end of their service life.
5. Examination and Hose Failures
Develop a protocol for inspecting hoses after each use and maintain comprehensive records of inspections and any failures encountered. This data can inform future maintenance strategies and identify patterns of wear.
6. Rubber Sealing Mechanisms
Pay close attention to elastomeric seals, such as O-rings and gaskets, as they prevent leaks and ensure proper sealing between hose components.
The Bottom Line
Composite hoses are indispensable in industries reliant on fluid transfer applications. By following regular maintenance practices, such as visual inspections and functional tests, businesses can enhance their operations’ safety.
Adhering to replacement intervals further optimizes the longevity and efficiency of their composite hoses. By investing in maintenance, companies demonstrate their commitment to compliance, safety, and cost-effectiveness, ultimately bolstering their reputation as responsible industry players.